Marine production facilities present unique challenges when it comes to surface preparation. When you are out at sea, you are exposed to the elements, which can hinder your blasting operations if you are not adequately prepared for them.
Airblast AFC has engineered blast rooms specifically for marine production facilities that protect against the most common factors, which we will discuss below.
Flash Rusting
Flash rusting is not your typical corrosion. It occurs when water resides on a layer of steel before the surface is coated, bleeding into the coating and producing a stain. This risk is greater on marine production facilities as the sea air contains a high level of moisture. Airblast AFC’s marine production facility blast rooms are engineered to allow for fine control over environmental conditions, eliminating the chances of flash rusting occuring.
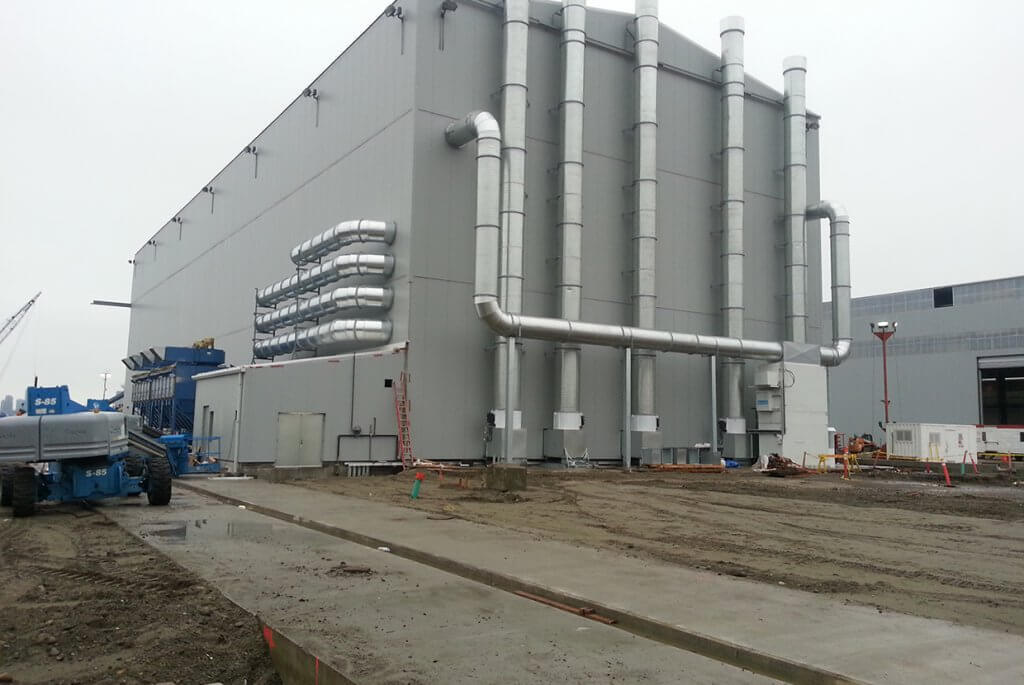
Paint Blistering
Paint blistering is another problem that arises during surface coating in marine production facilities due to the wet conditions at sea. As paint dries on a damp surface, adhesion of the paint to the surface is lost, causing the paint to bubble and blister. The marine production facility blast rooms developed by Airblast AFC allow you to carefully control both humidity and temperature to ensure that the chances of paint blistering are reduced.
Delamination
Delamination is the phenomenon whereby paint begins to peel away layer by layer and is caused, again, by wet conditions. Water can prevent adhesions between separate layers of paint, or it can occur within a layer of paint. Either way, the integrity of the surface coating is compromised. By using a blast room developed specifically for marine production facilities, your chances of delamination occurring are minimized.