Wind turbines are increasingly being found across the country as a reliable and sustainable method of power generation.
However, protecting the moving parts of the wind turbine itself can be a tough challenge. Preparing the surfaces for coating is an essential part of turbine maintenance. However, this process can be difficult given the size of wind turbine components.
The logistical challenges of blasting for wind turbine tower components requires special design elements that provide added functionality over standard blast rooms. Here, we will discuss the benefits of each.
Improved Ventilation and Automated Blasting
The increased ventilation functionality of our wind turbine tower facility surface preparation facilities keeps dust airborne so it can be carried away from the surface, preventing it from resettling.
Airblast AFC supplies blast robots for efficient blasting of the large wind tower turbine body. These machines provide consistent cleaning and surface preparation performance and are far more efficient than manual blasting.
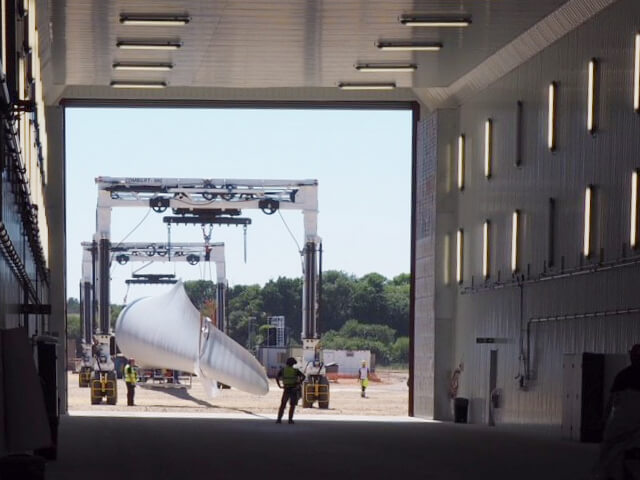
Temperature Control
Airblast AFC wind turbine leading edge treatment facilities are temperature controlled by an innovative system that safely recirculates heated air to avoid prohibitively expensive fuel costs. This allows for fast, affordable coating at the required temperatures.
Custom Design
The logistical requirements of wind turbine tower facilities mean that a custom-built solution is often the best approach. Airblast AFC is proud to assist operators of wind turbine tower facilities to improve their surface preparation, paint spraying, and leading-edge protection operations with custom built blast rooms.