> Blast Solutions / Media Recovery / Portable Garnet Recycler
Portable Garnet Recycler
The RC-50-150 is an abrasive recycling system which can be used inside or outside. Several types of reusable abrasive can be recycled by the RC-50-150 into builder's bags or blast vessels.
Grit Recycling System, commonly known as Garnet Recyclers
Contaminated media is deposited into the elevator hopper from where it is conveyed to a rotary sieve system. The sieve can be fitted with either Ø 4, 5 or 6mm holes as required. All oversize contamination such as coating scale, woodchips, glass, etc. are separated through sieve. The sieve also incorporates a dust exhaust connection which eliminates dust particles from the abrasive. After the sieve abrasive is run through an air wash. This can be adjusted to determine the particle size (spent abrasive) to be removed. All contamination including dust is deposited in bulk bags or if specified collection drums. Clean abrasive is directed to a storage hopper from where it can feed blast machines or bulk bags.
RC-80-160 Grit Recycling System
The RC-80-160 is an abrasive recycling system that can be used inside or outside. Several types of reusable abrasive can be recycled by the RC-80-160 into big bags or blast vessels. The rate of recycling depends on the type of abrasive being processed.
Operating principle:
Dust laden air enters through the inlet plenum of the collector, where heavy particles fall immediately into the hopper. As the air flows through the filter cartridges, dust is deposited on the outside of the filtering media. The filter cartridges are cleaned automatically and continually without interrupting the operation of the dust collector. An adjustable timer controls the cycle time. Solenoid valves introduce jets of high- pressure air into the cartridges in turn, through the Venturi opening above each cartridge. The resulting reverse airflow cleans the filter cartridges. Dust removed from the filter surface settles into the hopper. As each pair of filter cartridges is cleaned in succession, the remaining stays.
The used abrasive has to be put into the abrasive hopper, then it comes in a regulated flow to the elevator. From the elevator it comes in the rotary sieve, with holes Ø 4, 5 and 6mm at choice, if the abrasive is polluted with big parts like coating scale, woodchips, glass, etc. these contaminants are separated through the rotating movement of the sieve. The sieve is supplied complete with a dust exhaust connection. After the sieve the abrasive flow is through a cascade system.
The air wash action can be regulated to control the size of the reusable abrasive. Dust and non-usable (too fine) abrasive are automatically discharged and collected in big bags or extracted by the separate filter. The cleaned abrasive will fall into the abrasive silo and is ready to be stored into big bags or into blast vessels.
The system is supplied complete with: crane hooks, inspection covers and flexible dust-exhaust ducting to the big bags.
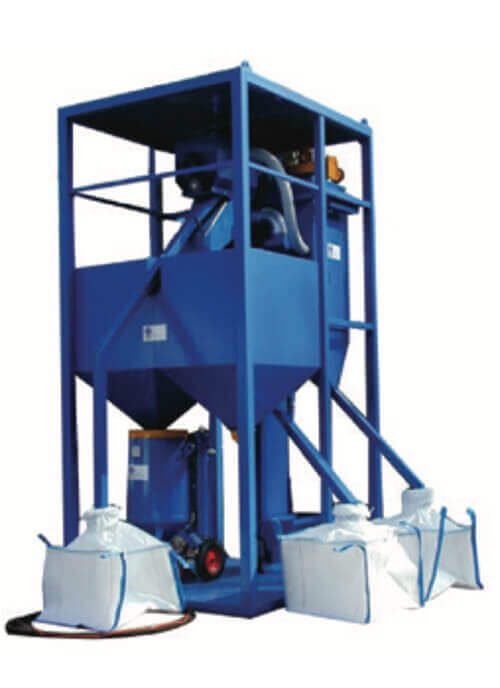
Technical specifications | Dimensions (in standing position): |
---|---|
Height: | 4780mm |
Width: | 2180mm |
Depth: | 2180mm |
Weight (empty): | 3000kg |
Total electrical power: | 2.75kW 400 Volt – 50/60Hz |
Compressed air: | 5bar |
Capacity silo: | 1600ltr |
Capacity elevator: | 4800ltr |
> for steel grit this is 4.5 x 4800/1,000 = 21ton/hour
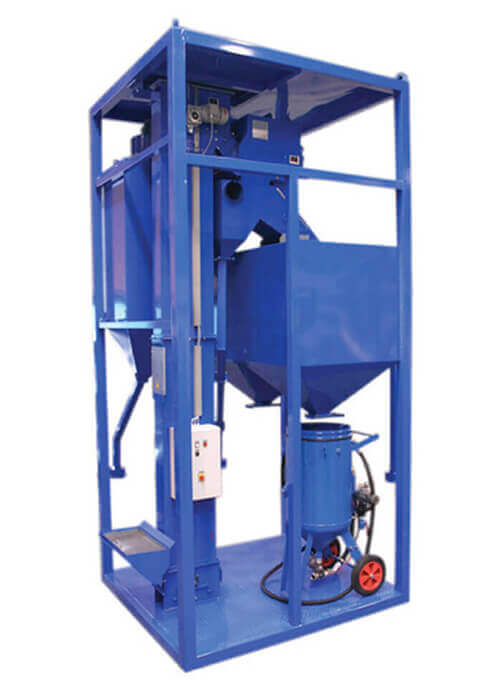
RC-50-150 Grit Recycling System
The RC-50-150 is an abrasive recycling system which can be used inside or outside. Several types of reusable abrasive can be recycled by the RC-50-150 into bigbags or blast vessels. The rate of recycling depends on the type of abrasive being processed.
Operating principle:
Dust laden air enters through the inlet plenum of the collector, where heavy particles fall immediately into the hopper. As the air flows through the filter cartridges, dust is deposited on the outside of the filtering media. The filter cartridges are cleaned automatically and continually without interrupting the operation of the dust collector. An adjustable timer controls the cycletime. Solenoid valves introduce jets of high-pressure air into the cartridges in turn, through the Venturi opening above each cartridge. The resulting reverse airflow cleans the filter cartridges. Dust removed from the filter surface settles into the hopper. As each pair of filter cartridges is cleaned in succession, the remaining stay.
The used abrasive has to be put into the abrasive hopper, then it comes in a regulated flow to the elevator. From the elevator it comes in the rotary sieve, with holes Ø 4, 5 and 6mm at choice. If the abrasive is polluted with big parts like coating scale, woodchips, glass, etc. these contaminants are separated through the rotating movement of the sieve. The sieve is supplied complete with a dust exhaust connection. After the sieve the abrasive flow is through a cascade system.
The air wash action can be regulated to control the size of the reusable abrasive. Dust and non-usable (too fine) abrasive is automatically discharged and collected in big bags or extracted by the separate filter. The cleaned abrasive will fall into the abrasive silo and is ready to be stored into big bags or into blast vessels.
The system is supplied complete with: crane hooks, inspection covers and flexible dust-exhaust ducting to the big bag
Technical specifications | Dimensions (in standing position): |
---|---|
Height: | 4780mm |
Width: | 2180mm |
Depth: | 2180mm |
Weight (empty): | 3000kg |
Total electrical power: | 2.75kW 400 Volt – 50/60Hz |
Compressed air: | 5bar |
Capacity silo: | 1600ltr |
Capacity elevator: | 4800ltr |
> for steel grit this is 4.5 x 3.000/1000 = 13.5ton/hour
RC-50-20 Grit Recycling System
The RC-50-20 is a mobile abrasive recycling machine which can be used inside or outside. Several types of reusable abrasive can be recycled by the RC-50-20, the rate of recycling depends upon the type of abrasive being processed. Used abrasive is manually fed into the intake hopper from where it is collected by
the bucket elevator and transported up the funnel. At the top of the funnel the abrasive is poured onto the spreading plate which ensures an even, shallow and wide flow down into the cascade cleaner. Inside the cascade cleaner the larger particles are separated into a dust bag, and the smaller particles are extracted by a separate cartridge filter which features solenoid controlled automatic pulse cleaning. Depending upon which abrasive is being recycled, the unit can be adjusted to ensure that the abrasive flow and particle separation are
fine-tuned to be as effective as possible. The cleaned abrasive is deposited into a hopper ready for reuse. The unit is manufactured in Europe from 3mm and 5mm steel to the highest quality standards. The motors and gearboxes are sealed and lubricated for life. The unit requires an electrical connection of 400volts – 50Hz as well as compressed air.
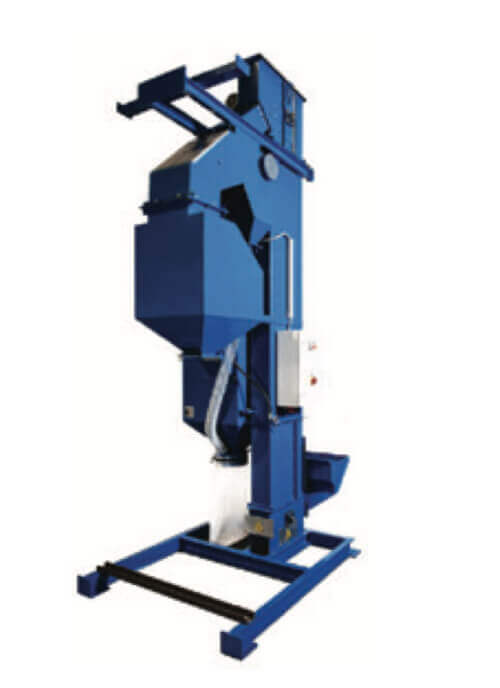
Technical specifications | Dimensions (in standing position): |
---|---|
Height: | 4.0mm |
Width: | 1.5mm |
Depth: | 1.8mm |
Weight (empty): | 650kg |
Vaculift Recovery System
With its high recovery rate, the Vaculift unit is an ideal system for in-house blasting operation.
Rapid Recovery Large Capacity Abrasive Storage Elevators
These systems are ideal for high volume media use and storage.
Auger Screw Recovery Systems
Our Auger Screw Recovery systems are great for high volume abrasive media use.
AbVac Abrasive Recovery Unit
The portable AbVac is an suction unit designed for the collection of abrasive into a bag.
Pneumatic Recovery
Pneumatic abrasive recovery systems may also be used with friable abrasives.
Portable Airvac Abrasive Vacuum
The Airvac with Cyclone Separator is a compact air-operated vacuum system that recovers abrasives for recycling.